1. Full-automatic measurement for comprehensive parameters of cylindrical thread plug gauges, cylindrical thread ring gauges, taper thread plug gauges, taper thread ring gauges, plain ring gauges, plain plug gauges and other gauges with internal & external dimensions, including virtual pitch diameter , single pitch diameter, basic pitch diameter, major diameter, minor diameter, thread pitch, thread angle, half of thread angle, flank straightness, lead angle, taper, etc.
2. Can measure trapezoidal thread gauges, buttress thread gauges, sawtooth thread gauges and other large-slope thread gauges.
3. Can measure comprehensive parameters of single thread and multiple thread.
4. Measure various thread gauges according to GB, ISO, BS, ANSI, DIN, JIS, API standards. With comprehensive and professional thread standards in database, it meets requirements of most customers.
5. Automatically generate test report according to selected standard.
6. After once measurement, the software can records various parameters of thread and display data of any position, in addition it generates the thread curve, relevant parameters and analysis chart automatically.
7. Measuring probe and workholder are identified automatically, which avoids collision of measuring probe caused by misoperation.
8. One-sided or two-sided measurement and analysis for gauges.
9. Controller for measuring pin positioning: with an easy-to-use buttons control box, the operation is more flexible.
10. User-friendly English software system and simple & convenient operation.
11. Test results are saved automatically with name of measuring series number + size of measuring gauge + type of measuring gauge, which can be recognized easily. With centralized database management for measuring records, the user can query and manage the measuring records according to object type, testing institution, manufacturing number, inspector, submitted institution, equipment number, inspection date, effective date, etc.
12. Can print multiple selected test records or test certificates from database at once time.
13. Can export test data to Word, Excel, AutoCAD (optional) files.
14. Data backup and restore.
15. Output reports in a variety of formats in Word or PDF, particularly the format can be customized.
16. Support user-defined standards.
Photo
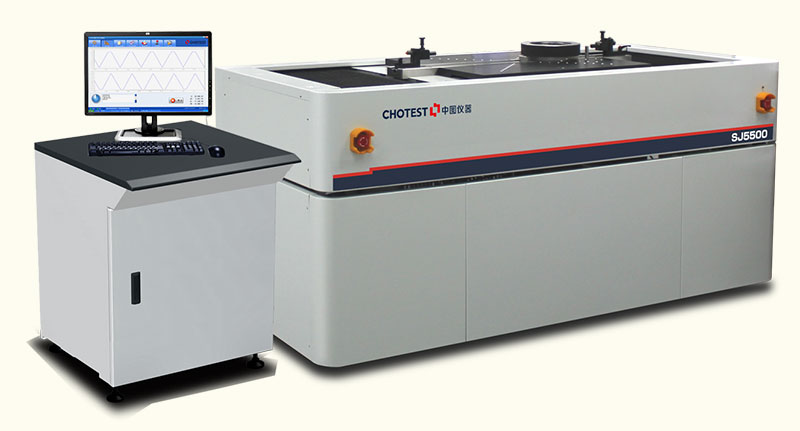
Parameters
Item No. |
SJ5500-200 |
Outside measuring range |
(1.0-250)mm |
Inside measuring range |
(2.5-250)mm |
Max measuring length |
250mm |
Min thread pitch |
0.1mm |
Weight |
2000kg |
Dimension |
200×90×91cm |
Measuring uncertainty: |
Cylindrical or Taper ring gauge(Mimor diameter >2.5mm, half of thread angle ≥27°) |
Minor diameter(μm) |
3.0 + L/200 |
Pitch diameter(μm) |
3.0 + L/200 |
Thread pitch(μm) |
0.8 + L/200 |
Cylindrical or Taper plug gauge (Major diameter >1.0mm, half of thread angle ≥27°) |
Major diameter(μm) |
2.9 + L/200 |
Pitch diameter(μm) |
2.9 + L/200 |
Thread pitch(μm) |
0.8 + L/200 |
Plain ring or plug gauge(μm) |
2.0 + L/200 |
Other measurement(μm) |
2.0 + L/200 |
Contour measurement |
Outside measuring range |
(0-250)mm |
Inside measuring range |
(2.5-250)mm |
Resolution of X-axis and Y-axis |
0.01μm |
Accuracy of X-axis |
±(1.5+L/100)μm |
Accuracy of Z-axis |
±(1.5+L/100)μm |
Max gradient |
75°(T-shaped measuring probe) |
Measuring force |
(40-150)mN |
Measuring speed |
(0.01-2)mm/s |
Description
SJ5500 achieves full-automated and precision measurement of comprehensive thread parameters by using precision linear encoder system, precision air bearing driving system, high-end servo motor control system, high performance industrial computer control system and large capacity memory technology. After driving the measuring probe to contact with workpiece by precision air bearing system, the software records the horizontal and vertical coordinates in measuring process by applying precision linear encoder system, then, on the basis of synthesizing the two-dimensional measuring values, the software calculates and obtains a variety of thread parameters according to relevant definitions from norms.
SJ5500 is a full-automated measuring machine. The operator only needs to install the thread gauge, select matching standard and input scanning length in software, then the system measures automatically after click the "start" button. The software displays real-time tooth profile curve of thread gauge, and calculate the major diameter, pitch diameter, minor diameter, thread pitch, thread angle, other thread parameters automatically. Finally the system qualifies a variety of thread parameters according to selected thread norm, and test report is generated automatically. The whole process is completed in 2 min.
Features
1. Full-automated measurement: Scan test objects and display all values in 2 minutes without manual intervention and calculation. According to selected thread standards, the system generates the test report finally. That significantly simplifies the operator's work, as well as improves the measuring efficiency, quality and accuracy.
2. Resolution is 0.01um; High accuracy, high stability and high repeatability.
3.Simple, humanized design: Thanks to quick workholders for thread, object installation is very simple and easy. Due to user-friendly software interface, the operator can be trained to use it within a few minutes. Operation of the machine is extremely simple.
4. 3D navigation function(Patent No.1): Greatly improve the operating convenience, accuracy, safety and reliability.
5. Convenient and accurate replacement of measuring pin(Patent No.2): Thanks to innovative structure for probe installation, the probe is fixed easily and simply. This structure eliminates errors caused by repeated installation, which guarantees excellent repeatability.
6.Combined workholder(Patent No.3): Thanks to two-in-one and three-in-one workholders, gaskets and heel blocks are not required. These workholders can be used for measuring both thread ring and plug gauges, which makes work more simple and efficient, moreover reduces risk of misoperation.
7. Ingenious balancing mechanism(Patent No.4): Thanks to ingenious balancing mechanism, the problem of Z-axis swing while X-axis movement is solved completely, which ensures the stability of the coordinate system during scanning, consequently measuring accuracy is improved.
8. Accurate & sensitive measuring force system
Measuring force automatically varies from 0.01 ~ 0.10N according to different gradient during scanning. Thanks to micro measuring force, measuring pin is almost abrasion-free, so lifespan of probe is very long, in addition test objects are protected as well. The micro measuring force also greatly helps to achieve measurements for steep-slope thread gauges.
Applications
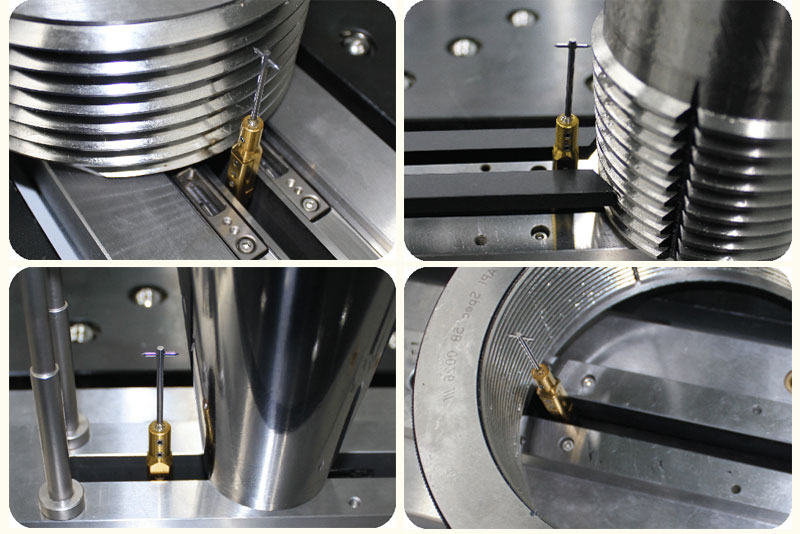
Can measure:
Thread plug gauge
Shell thread plug gauge
Thread ring gauge
Shell thread ring gauge
American Standard unified thread gauge
55 ° non-sealing pipe thread plug gauge
55 ° non-sealing pipe thread ring gauge
Thread sealing pipe thread with Regulation (RB)
Wei's taper pipe thread gauges
Brunel taper pipe thread gauges
ACME taper pipe thread gauge
DIN thread gauge
JIS thread gauge
Special thread gauges for gas cylinders
ACME cylinder pipe thread gauge
API SPEC 5B series gauge:
Oil pipe thread gauge
Oil pipe taper gauge
Oil pipe taper master gauge
Oil casing thread gauge
Oil casing taper gauge
Oil casing taper master gauge
Oil pipeline gauge
API SPEC7-2 series gauge:
Numeric oil drill pipe joint thread gauge
Numeric oil drill pipe joint thread master gauge
Regular type oil drill pipe joint thread gauge
Regular type oil drill pipe joint thread master gauge
Full bore type oil drill pipe joint thread gauge
Full bore type oil drill pipe joint thread master gauge
API SPEC 11B series gauge:
Rod thread gauge
Double pin plug gauge
Double taper plug gauge
Incompetence plain plug gauge
Plain master ring gauge
Trapezoidal thread plug gauge
Configuration
Standard configuration
1. SJ5500 host machine
2. Workholders
3. Jacking fixture
3. Measuring pins group
4. Standard thread gauges
5. Standard plain ring gauges
6. Standard plain plug gauges
7. Built-in regulations and standards
8. Testing software
9. Computer
10. HP color laser printer
11. Aluminum alloy box for accessories
12. User manual
13. Product certification and warranty card
Optional configuration
1. Software module for trapezoidal thread measurement
3. Measuring pins for trapezoidal thread measurement
4. Software module for profile measurement
5. Measuring tips with spherical face
6. Other workholders
7. Water-free, oil-free, silent air supply system
8. Electronic moisture-proof case